Remote Service
SortiPack® grades, sorts and packs fruits and vegetables worldwide, working with fresh produce from a greenhouse. Uptime and continuous production are therefore critical, so what to do when a problem occurs?
Our products are built to last, with top quality components and designed with a focus on ensuring continuous production. However, as with any machine, sometimes malfunctions might occur. SortiPack® is designed to minimize the impact of any issues, and to get you back to full capacity quickly using remote service.
Crux Agribotics has experienced specialists who can quickly solve over 85% of problems remotely. And if on-site assistance by our local service partners is still needed, we can monitor remotely and assist them while they work.
How does remote service work?
With our remote service, we can offer support for malfunctions and questions anywhere in the world via a secure connection. Using log data, real-time data and cameras inside and around SortiPack®, we can respond quickly and efficiently and take immediate action if necessary. And if needed, we monitor remotely to identify potential issues before they become a problem.
Our Services team has a SortiPack® in-house at the workshop in Eindhoven which allows us to simulate problems and show the right solution. This way we can support our customers worldwide the fastest and solve problems quickly and effectively.
After years of production at various sites, remote service has ensured time and time again that SortiPack® could quickly function at full capacity again after a malfunction. Read about some examples here:
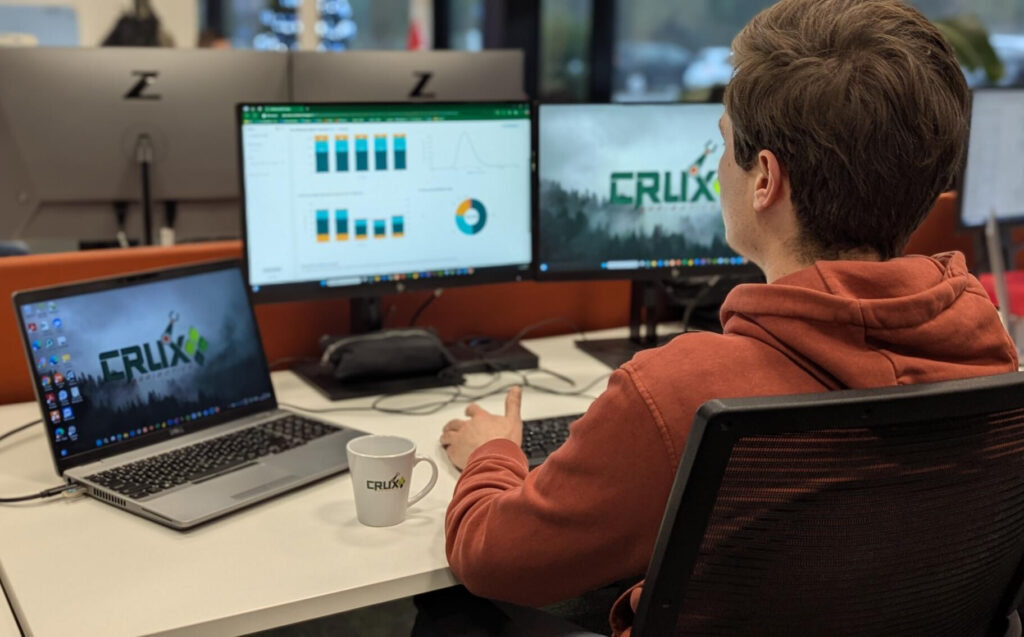
"Contact with Crux is pleasant, remote service helps us resolve anything quickly and easily."
Case 1: Robot error
1 of the 9 robots of a SortiPack® in France had problems starting up. Fortunately, the modular setup of the SortiPack® ensured that the other robots could continue at full speed. However, the reduction in capacity would lead to delays. Therefore, it was important to have the 9th robot back online as soon as possible.
The service engineer on duty in Eindhoven established a secure connection with the SortiPack® in France, allowing him to view the data and watch via camera images. He concluded that the robot arm was in the wrong position.
The cause? After a small maintenance check earlier, the robot arm had not been correctly set back into position by the operator. Our engineer instructed the operator on how to place the robot arm in the correct position, while watching via the built-in camera to verify that the instructions were being followed correctly.
To prevent this from happening again in the future, our engineer then provided helpful tips. This way the operator on site knows exactly what to do should this event occur again, so he can solve the problem independently.
This quick action allowed the SortiPack® to resume the sorting process within 10 minutes of contacting Crux Agribotics Services.
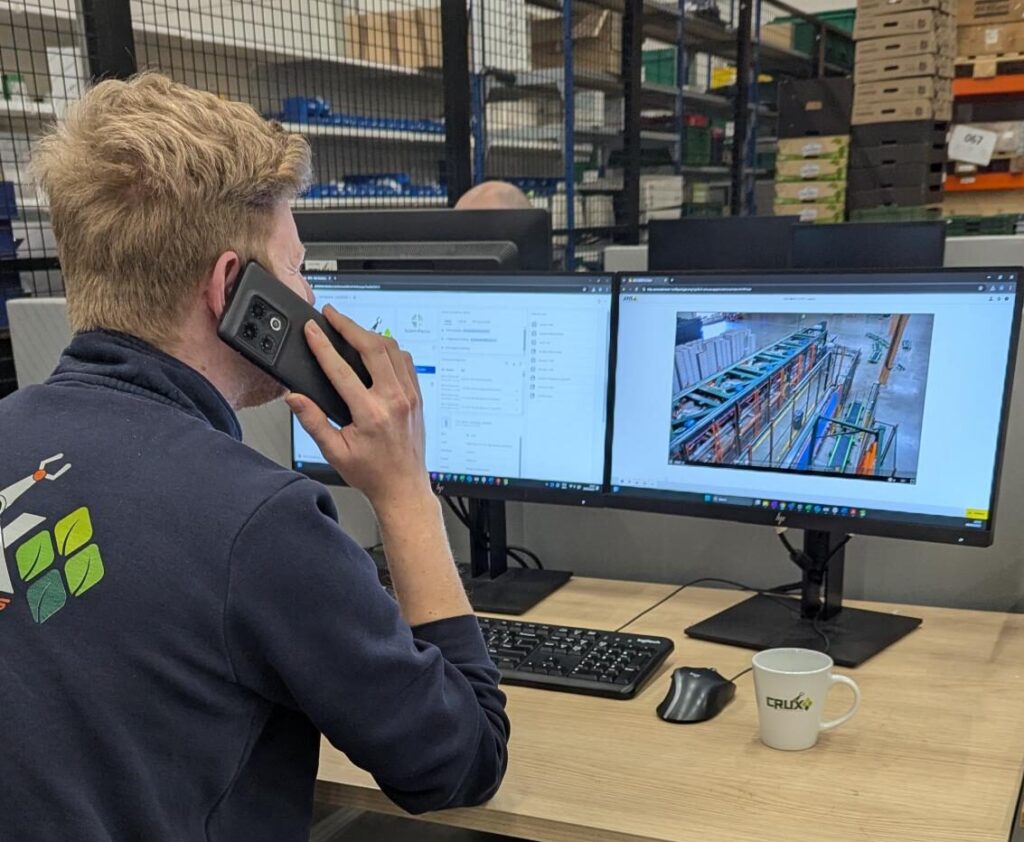
Case 2: Performance decrease
Our team received a notification from a customer located a few hours away from our headquarters. The infeed system which provides the supply of product to the SortiPack® was no longer operating at the correct speed. This allowed the customer to continue running, but at a reduced capacity.
After a brief phone conversation with the customer, the engineer on duty looked at the data remotely and discovered that the chain of one of the motors was insufficiently lubricated. This caused too much resistance on the chain and caused the motor to not run optimally.
The solution was simple but effective: we advised the customer to lubricate the chain properly and indicated where they could access the chain. After performing this maintenance operation the motor quickly recovered its optimal performance. The infeed system was able to operate at full capacity again, allowing the SortiPack® to function smoothly and efficiently again.
The remote monitoring and simple solution meant there was no waiting time for a Field Service Engineer to arrive on location and the customer was able to resolve the issue within 30 minutes of contacting Crux Agribotics Services.
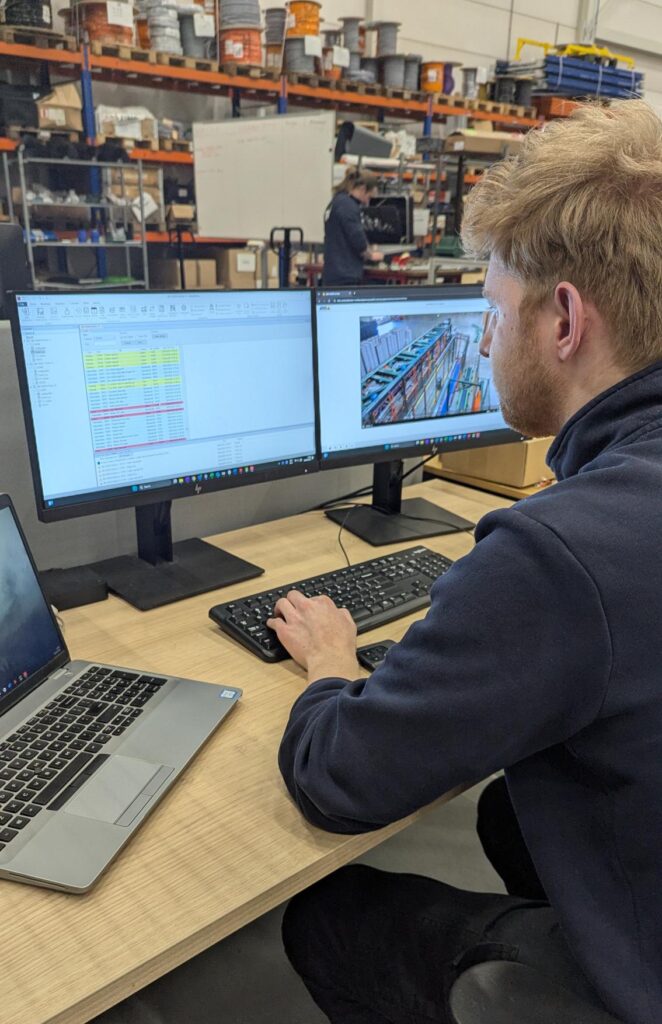
Case 3: Communication error
The operator of a foreign customer site received a warning on the dashboard of their SortiPack® and called our service number. The warning indicated that there was no communication with one of the robots. Due to the lack of communication with one robot, only eight robots could operate simultaneously instead of all nine, resulting in a reduced sorting and packing speed.
The service engineer on duty logged in remotely to view the SortiPack® logbook. He noticed that the connection between the SortiPack® and the robot in question was lost several times. The engineer suspected that there was a problem with the internet cable connecting the robot to the rest of the system.
To solve this problem quickly, the engineer suggested using an internet cable that was available on site to test if the connection could be restored. To help the operator with replacing the cable, he sent photos and monitored via a remote camera with a secure connection.
This solution proved effective: the robot was able to rejoin the other eight robots, returning the process to full capacity again. The engineer monitored everything remotely and ensured that during the next scheduled on-site maintenance, the cable would be correctly and neatly installed in the SortiPack®.
This easy and simple temporary solution allowed the client to return to full capacity very quickly.
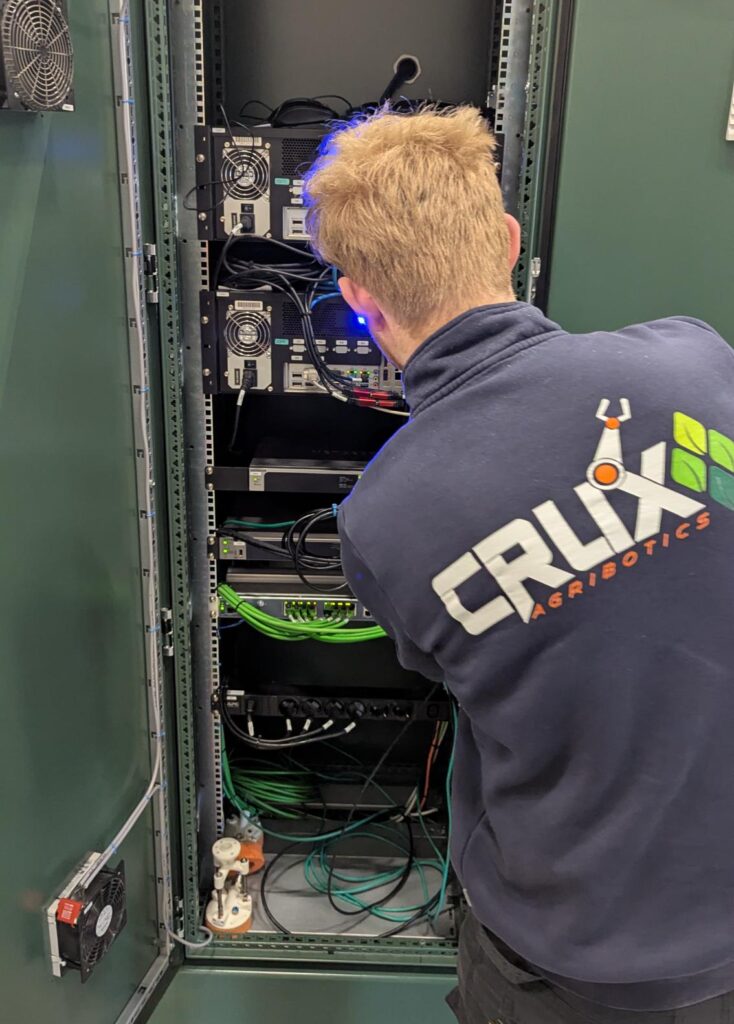