SortiPack® Beef Tomato
Beef tomatoes are prone to post-harvest damage due to punctures and bruising and require gentle handling. The sorting and packing process is labor-intensive which brings many challenges: labor costs and scarcity, worker management and virus risk.
SortiPack® decreases labor, damage and weight giveaway, so beef tomato growers can focus on their produce.
The SortiPack® system for beef tomatoes scans and classifies tomatoes directly from the harvest crates, eliminating the need to tip the crate and risking damaging the fruit. Robots gently pick the tomatoes from the harvest crates and pack them into the correct customer packaging.
SortiPack® can simultaneously pack multiple packages for different customers and select tomatoes by weight, size and color class. Completed customer packages are transported to the palletizing area and empty harvest bins are stacked and automatically redirected to the harvest carts for re-use.
The AI algorithm divides tomatoes into the best possible packing combinations. This results in a more uniform looking customer packaging and lower weight giveaway compared to manual packing.
“We’re very happy with SortiPack, it helps us save a lot of labor. We now have SortiPacks running at 3 different locations”
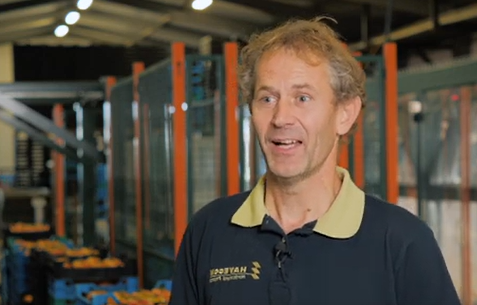
PLAY VIDEO
Advantages of SortiPack® Beef Tomato
SortiPack® Beef Tomato uses vision, AI and robots to transport tomatoes directly from harvest crates into customer crates or boxes. It can sort by weight, size and color and fill customer crates and boxes in an optimized way, staying consistent all day, every day.
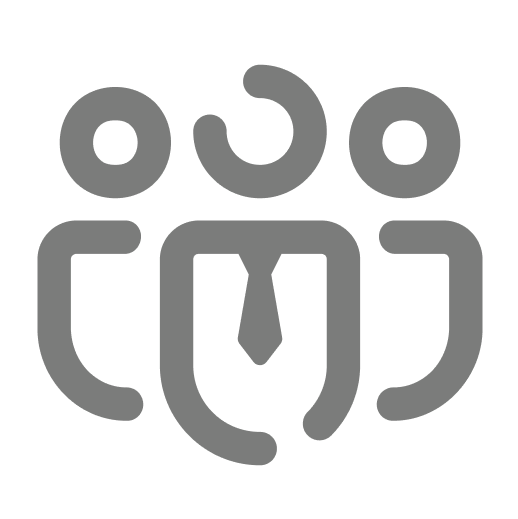
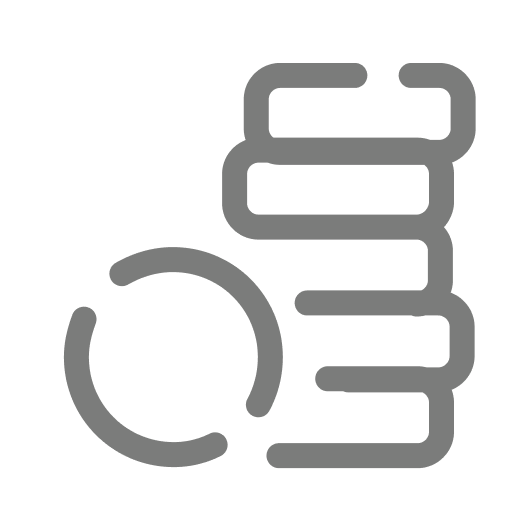
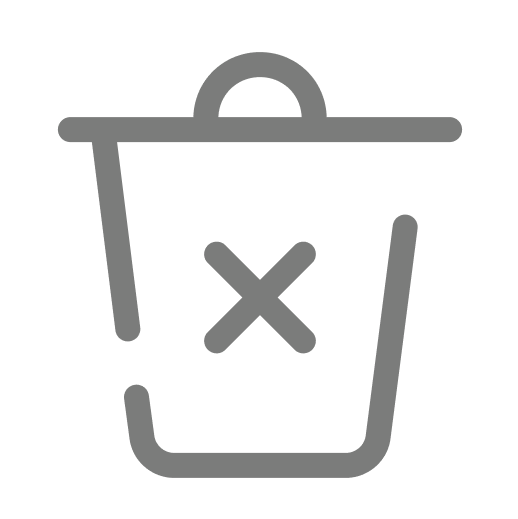
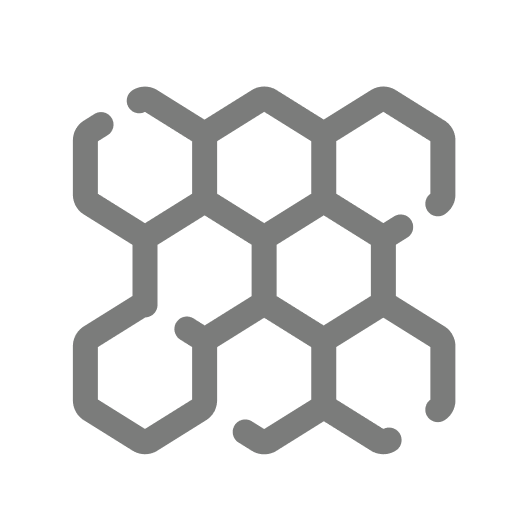
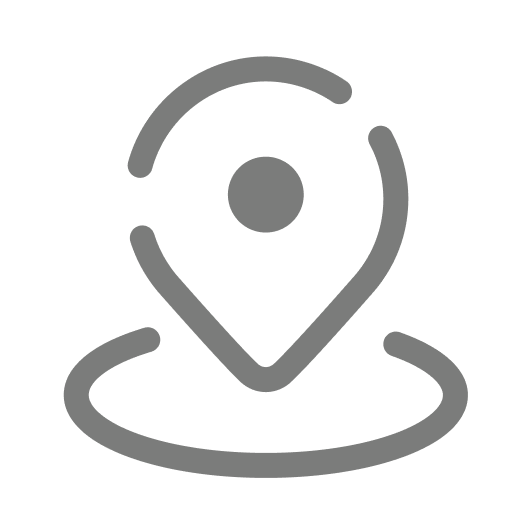
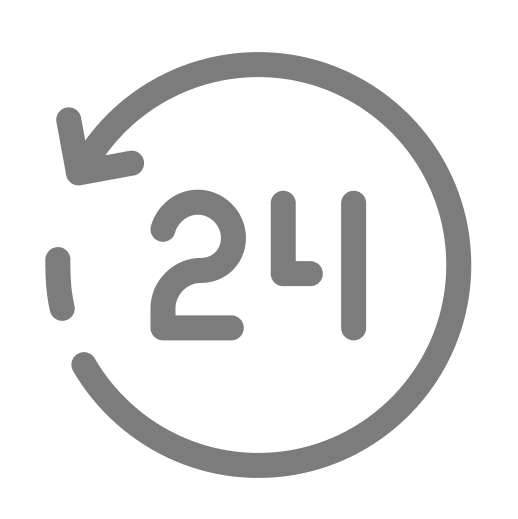
Save on labor - reduce giveaway - no damage - track & trace
Our offering
With our end-to-end platform we digitize greenhouse horticulture to enable data driven, predictable, controlled and scalable growth of fruits and vegetables.